Abbiamo voluto testare duramente la resistenza del titanio... Vediamo come è andata!
Prima di capire perché abbiamo schiacciato un ITE con una Mercedes, facciamo un passo indietro e comprendiamo insieme qual è il miglior materiale (ed il più resistente) per costruire un endoauricolare.
Negli anni 80/90 i materiali utilizzati per la costruzione degli endoauricolari comprendevano anche l’oro e l’argento. Questi materiali, nonostante la loro natura duttile e malleabile, comportavano nel processo produttivo grosse problematiche, in quanto si rendeva necessario utilizzare sostanze pericolose nella fase di galvanizzazione.
Qui sotto potete vedere alcuni dei primi endoauricolari galvanizzati in oro dagli archivi storici di CRAI.
Dopo l’oro e l’argento - che ad oggi avrebbero costi proibitivi - la produzione degli ITE avviene utilizzando una particolare resina medicale anallergica, un materiale decisamente più versatile utilizzabile anche nel processo di produzione con stampanti 3D.
Ma qual'è il materiale migliore ad oggi per la realizzazione di un ITE?
Da diverso tempo nel mercato audioprotesico si parla di endoauricolari in titanio.
Il titanio è un materiale leggero e molto resistente, noto inoltre per la sua biocompatibilità con il corpo umano. Questo lo rende un materiale ideale per la realizzazione di apparecchi acustici ITE e - come ben sappiamo - per tutte le protesi in generale.
Una caratteristica peculiare del titanio è che si adatta immediatamente alla temperatura corporea. Molti pazienti che utilizzano endoauricolari in titanio affermano che l'apparecchio acustico "sembra scomparire all'interno del condotto uditivo".
Inoltre, grazie alla sua risaputa resistenza, consente di ridurre lo spessore delle pareti del guscio di 1/3 rispetto alla resina, rendendolo più leggero e riducendo sensibilmente la sensazione di “pienezza auricolare” che alcuni pazienti possono lamentare nell’utilizzo di un endoauricolare.
Ne risulta quindi un endoauricolare più leggero, resistente e con un design davvero accattivante!
Il processo "Titanium Shell" di CRAI per garantire la massima soddisfazione del paziente.
Da molto tempo in CRAI stavamo lavorando per fornire questo tipo di prodotto, ma con un obiettivo ben preciso: garantire una produzione veloce del guscio in titanio.
Obiettivo raggiunto: riusciamo a realizzare un endoauricolare in titanio in soli 8 giorni lavorativi!
Come? Producendoli direttamente in Italia, più precisamente a Padova!
Abbiamo ideato inoltre un processo di produzione denominato TITANIUM SHELL, che prevede la realizzazione di un guscio in resina di “prova” per verificare che rispetti totalmente l'anatomia dell'orecchio del paziente, per poi procedere alla realizzazione del vero e proprio guscio in titanio.
Riassumendo il processo Titanium Shell:
- Presa di Impronta del Paziente
- Digitalizzazione del'Impronta
- Realizzazione del "Guscio Prova" in resina
- Test da parte del paziente del "Guscio Prova"
- Scelta del colore
- Realizzazione del guscio Titanium Shell
UNA NUOVA GAMMA DI COLORI UNICI!
Garantire la totale personalizzazione del prodotto era un altro dei nostri obiettivi.
Abbiamo studiato un processo di produzione che consenta la scelta di un'ampia gamma di colori del titanio, garantendo al paziente di ottenere un prodotto unico realizzato in base ai suoi gusti, creando così un vero e proprio oggetto di design su misura!
Ecco alcuni dei colori disponibili!
Arriviamo al dunque, abbiamo veramente schiacciato un endoauricolare in titanio con una mercedes? Certo, per testare la resistenza del titanio!
Ecco il filmato, buona visione!
Da oltre 40 anni il nostro obiettivo è assistere gli Audioprotesisti nella loro quotidianità.
Mettiamo a tua disposizione i nostri prodotti, le nostre metodologie di lavoro e i nostri servizi per permetterti di dare ai tuoi clienti le migliori soluzioni per la salute dell'udito.
Parla subito con uno dei nostri esperti e scopri cosa possiamo fare per te!
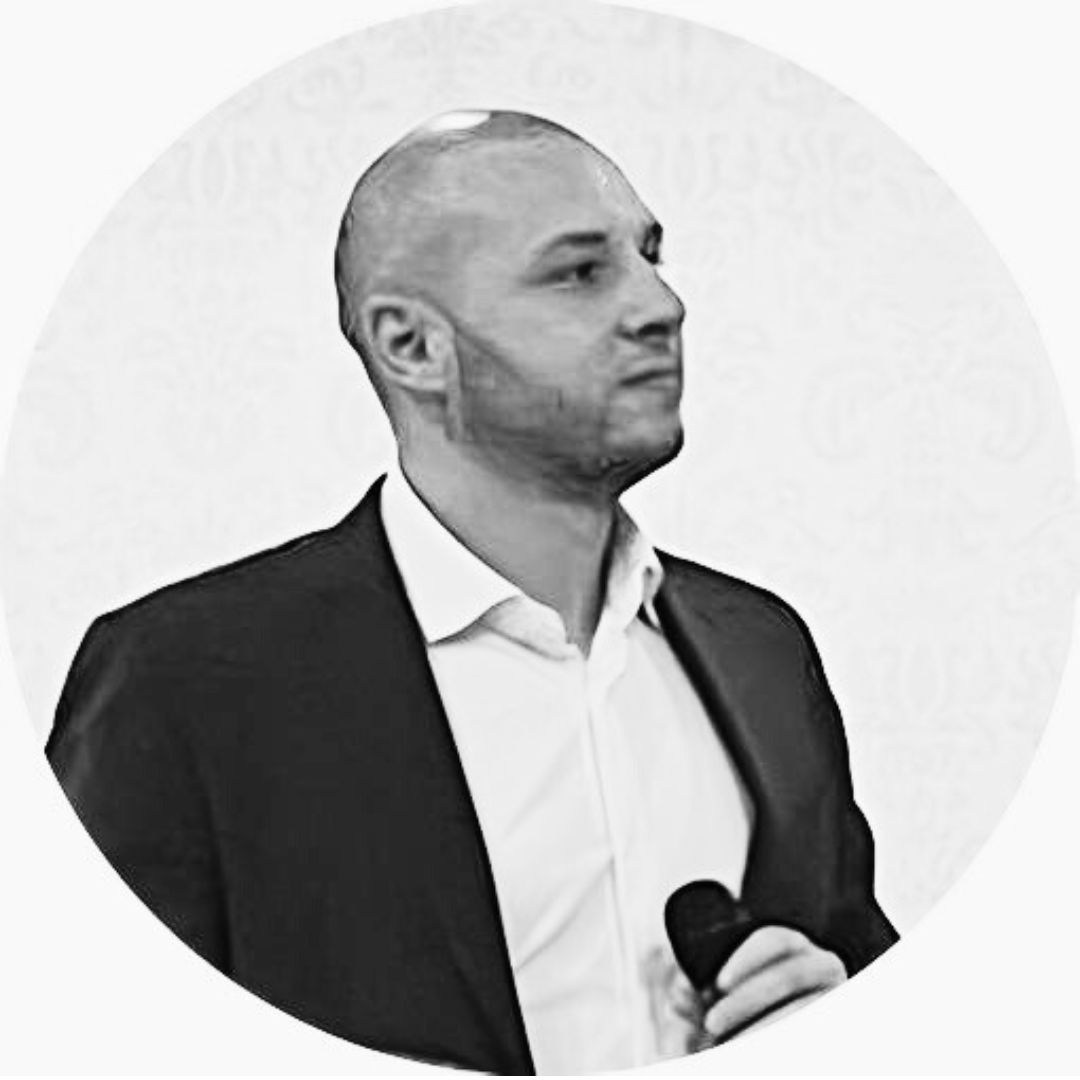